Work has been a traditional human activity for millennia, evolving into the many directions that needs and curiosity brings about. Since the industrial revolution, though, work is being channeled towards one direction: maximizing the collective productivity. The first implication of this redirection is the split between the worker and the work process, which is then subject of optimization for efficiency.
In the past, the worker and the process were indistinguishable. Since the worker was responsible for executing the whole process on his own, it was not possible to detach process from labor. Even if the worker was part of a collective association, there would be no division of tasks between the workers. In fact, the workers would do the same tasks together or in alternation.

The industrial revolution brought a different organization of work. Each worker had to specialize in a handful of tasks to be performed with the maximum efficiency. As factories grew in size and complexity, the tasks were broken down and workers had to become more and more specialized. At some point, workers lost the awareness for the entire work process and a new kind of specialized worker arose to take care of it: the manager.
The manager was a white-collar who oversee the blue-collar workers and also defined their way of working. He was freed out from the heavy duty of manual labor in order to keep the process going on. With the help of engineering, the manager could create new machines to improve the process, either by increasing control over the specialized workers or by automating certain tasks. The manager created and used knowledge to optimize work processes.
At the beginning of the XX century, Frederick Taylor publishes an influential paper criticizing the managerial knowledge for its basis on rudimentary rules-of-thumb and gut feelings. Taylor proposed that managerial knowledge could be based on scientific laws derived from the observation of workers on duty. At Bethlehem Steel company, Taylor observed pig iron workers with a stopwatch and introduced changes in their work process so that enough time was given to rest between the heavy loaded tasks. By following a fixed schedule of work and rest, the pig iron workers could achieve the maximum productivity at work.
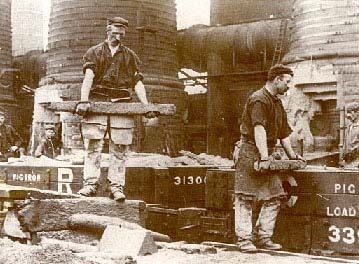
A step further in scientific management was undertaken by Frank Gilbreth, who employed video cameras to record and analyze work, what became known as motion studies. One of the studies done by Gilbreth aimed to find the “one best way to lay a brick”.
In a different but similar approach to management, Henry Ford introduces the assembly line to produce cars in 1913. Instead of workers moving around the factory, the product to be assembled was the one being moved. The physicality of the assembly line assured that the work tasks were well divided and streamlined accordingly. Strangely enough, Henry Ford got this idea from meat packing factories.
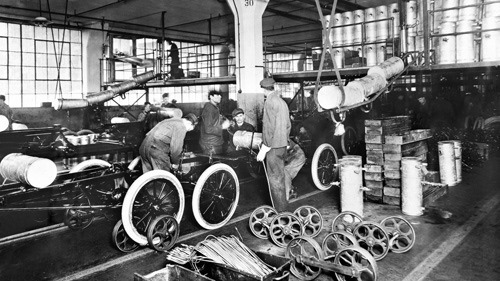
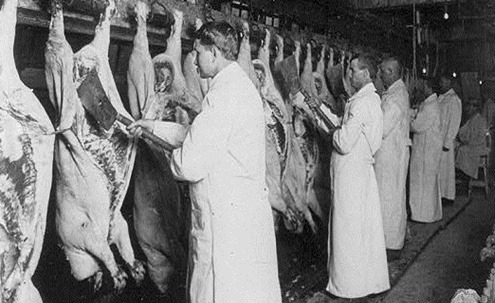
In the 1950s, Taiichi Ohno developed a more advanced version of the assembly line with the principle of just in time. Just in time means keeping the inventory low and replenishing only when there are requests by the next step of the production chain. The goal is to avoid the waste of resources as much as possible. In practice, this is accomplished by attaching and detaching identification cards (known as Kanban) to supply packages, which stands in place for new orders as well.
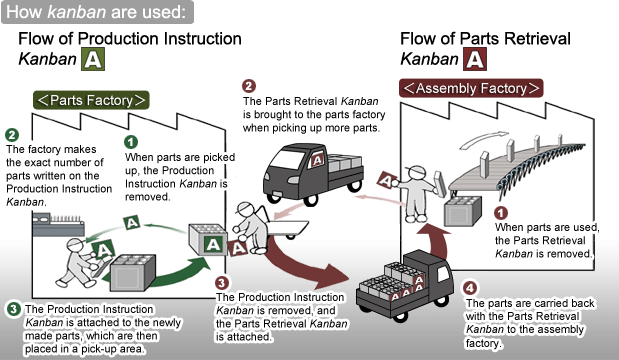
When brought to the United States in the 1980s, the Toyota production system was named lean manufacturing. A major breakthrough of lean was the formation of multi-purpose teams in which members would rotate tasks with one another. These teams are also empowered by the manager to make improvements to the work process by their own, what represents a major challenge to the industrial revolution split between worker and process and the consequent worker’s specialization.
The optimization of work processes in lean manufacturing takes into account the availability of highly-developed automation such as mechanical arms that can take over manual labor. The worker is expected to stay flexible to the constant inflow of new technologies and fluctuating market demands. In order to do so, the worker has to create and use knowledge as much as managers did in the past.
The principles of lean manufacturing has been adapted to industries beyond automobile factories. Perhaps the currently most interested industry in lean principles is software development. They are seen as a means to shorten the time to market, a crucial matter for startups.
The Kanban board is a popular technique derived from Lean and used by startups. There the workers define their own tasks and attach to the designed status area, indicating where they are in the process. The publicity of the board builds up process awareness between the workers, not just for the management. Everybody is supposed to be constantly watching for opportunities to optimize the work process.
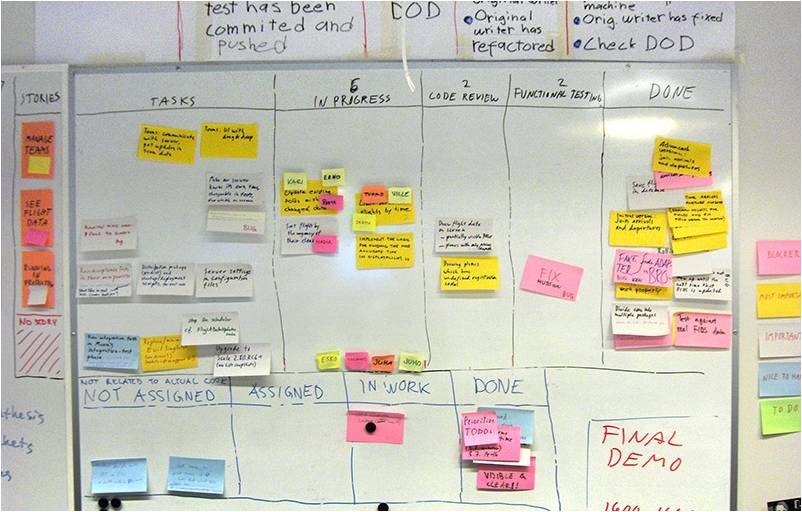
The optimization of work processes seems to be the next competitive edge in the nascent knowledge economy. However, time to market is just one of the factors for competition. More important than that is to produce remarkable innovations. Streamlining and distributing knowledge among the workers do not necessarily lead to remarkable innovations. For that, it is necessary to co-create new knowledge. A contradiction arises then since the co-creation of knowledge goes in the opposite direction of the optimization of work processes.
As explained in another post, knowledge cannot be mass produced like information. Knowledge requires going through long periods of sense making and relating, processes that cannot be optimized due to their subjective and inter-subjective nature. The creation of new knowledge is even less suitable for optimization since it is impossible to know what is being created and how it is being created before it starts.
This contradiction is perhaps being better dealt by the service industry. Service companies are improving their work processes through the co-creation of knowledge, as part of broader efforts to increase worker’s participation. Optimization is just one of the aspects considered. Next to it there is customer satisfaction, worker’s resilience, and organizational culture. The directions for the development of work are much more diverse than in other industries.
As an example, lean in healthcare is applied not only to process management but also to redesign the whole workplace. The workers achieve more self-determination than in lean manufacturing when co-creating knowledge about their own work. This socialization of the design space is motivated by the expansion of the design object, which can no longer be grasped by product-oriented design.
I have studied a project like that in my PhD, yet it was not successful in dealing with the contradiction mentioned above. We helped to organize a workshop with the healthcare professionals who are going to work in a future medical imaging center. The managers wanted them on board to optimize the work processes before the building is built as a means to raise motivation to sign up for the project. Our researchers from VISICO setup two instruments to optimize work processes: a healthcare simulator and a low-tech visualization.

Despite the moderate success of the workshops, the project failed to build up commitment with the participants. The healthcare professionals were more concerned about why and how the co-creation of knowledge would take place in the new center. Since they already had similar machines in the own hospitals, the motivation to join the center was completely other than what the project managers expected. Instead of organizing a workshop about the optimization of work processes, the project managers should have organized a workshop about the co-creation of knowledge to raise motivation.
One thing does not replace the other; however, trying to do them together fall back to the most equipped side, currently occupied by the optimization of work processes. Working towards the co-creation of knowledge requires courage to work without a guidance and accept the multiple directions that work can follow. With this courage it is possible to overcome the imperative of improving collective productivity and realize other means of being a better human through work.